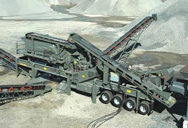
Roll Grinder Monitoring – Alta Solutions
Roll Grinder Monitoring. Steel and aluminum mills know that monitoring the roll grinding process for quality control improves the performance of work rolls and back-up rolls (BURs) used throughout the mill. Work rolls touch all product surfaces that pass through a mill. Therefore, any pattern or lead line on these rolls is imparted onto the ...
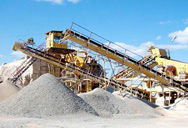
Chapter 18. Feed Milling Processes - Home | stone …
The mill is best used to crack whole grains with a minimum of "fines". It is not used as a final process for reducing the size of ingredients used in fish feeds. 2.5 Screening. Associated with grinding feeds for fish fry, a sieving system is required which classifies materials to any desired particle size.

Mill (grinding) - Wikipedia
A mill is a device that breaks solid materials into smaller pieces by grinding, crushing, or cutting. Such comminution is an important unit operation in many processes.There are many different types of mills and many types of materials processed in them. Historically mills were powered by hand (e.g., via a hand crank), working animal (e.g., horse mill), wind or water ().
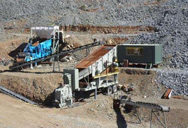
Noise Monitoring That Prevents Mill Damage | …
SAG mills are primarily used at gold, copper and platinum mines where steel balls are used for the grinding. The Manta Controls Advanced Control System, called the SAG Cube, automatically monitors and controls a SAG Mill, keeping track of critical process variables impacting mill throughput.
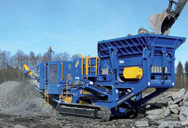
Roll-Bowl COP - A full featured mill monitoring …
Monitoring and Diagnostics. Data Collection The Roll-Bowl COP system contains the software and hardware necessary to collect and analyze coal pulverizer operating data, using both time-domain and frequency domain techniques, to reveal the dynamic conditions present within the mill without removing it …
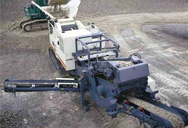
vertical roller mill in cement industry malaysia
The inauguration of the world’s largest vertical roller mill for cement grinding completes a smooth commissioning process at Shah Cement in Bangladesh With an 81metre grinding table and six grinding rollers powered by an 116megawatt gearbox the FLSmidth OK 816 Mill has milled its first cement at Shah Cement’s Muktarpur Plant
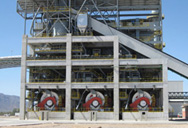
Crushing, Grinding and Reduction in stone Milling ...
THE EFFECT OF ROLLER MILL ROLLS TO GRINDING There are two types of roller mill rolls as Crushing roller mill rolls and reduction roller mill rolls; 1. Crushing roller mill rolls make an angle on rollers in order to fulfill the wheat cutting-opening, excavating- eroding and crushing and spliting missions, to do so, it has extending threads.
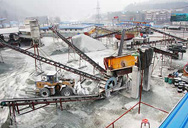
Cold Rolling Grinding | TENOVA
Pomini Tenova is the worldwide leader in the design and supply of Roll Grinders for flat product Rolling mills as well as of special machines for grinding of heavy components. Roll Grinder Heavy, Medium and Light Duty Fully Automatic CNC Roll Grinders assure superb performance in terms of tolerance and Surface finishing of all type of rolls, high reliability and internationally patented ...
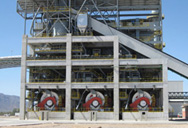
Finding failure - International Cement Review
Process-correlated torque monitoring allows plants to plan maintenance of the grinding rolls to avoid excessive dynamics in the roller press. In case study 2, following the change of the bearings of the grinding rolls, the plant team was looking for a way to reduce the risk of bearing failure.
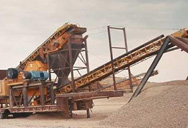
Rubber Roll Grinding | Precision Roll Grinders
PRG’s off-machine roll grinding is the key. For all aspects of the stone industry, off-machine roll grinding is better than in-place roll grinding. In-place (block) grinding is done in bearings on the machine, which does not produce rolls that meet the original specifications.
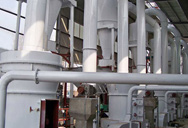
Roll Grinding - herkules-machinetools.com
Roll grinding to the highest standards With more than 100 years of experience, Herkules is the specialist in roll machining and a world leading manufacturer of roll grinders. The reason why customers worldwide rely on Herkules for their machining demands: pioneering machine technology combined with solutions tailored to the client’s needs.
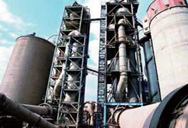
Three roll mill - Wikipedia
A three roll mill or triple roll mill is a machine that uses shear force created by three horizontally positioned rolls rotating in opposite directions and different speeds relative to each other, in order to mix, refine, disperse, or homogenize viscous materials fed into it.. The three-roll mill has proven to be the most successful of the range of roll mills which stone extensive development in ...
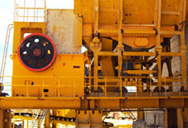
Defects of grinding mill - Mine Equipments
Mill-Roll-Grinding_Layout 1 - Magnetic Analysis Corp. Monitoring the Grinding Process of. Mill Rolls with Eddy Current compact cabinet that ... grinding to …
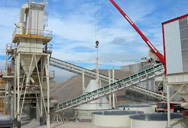
Basics of Grinding - manufacturing.stanford.edu
grinding machines perform the dressing task automatically. The application of coolants to the grinding process is important. Coolants reduce grinding machine power requirements, maintain work quality, stabilize part dimensions, and insure longer wheel life. Coolants are either emulsions, synthetic lubricants or special grinding oils.
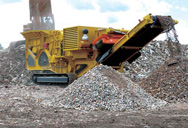
capacity of rolls grinding mill - janudema.nl
Apr 09, 2015· Grinding Mills and Their Types , The vibrating mill has a grinding chamber which is filled to around 65 % to 80 % of its capacity with grinding media such as balls or rods The chamber is vibrated at a frequency of between 1000 and 1500 times per minute (can be variable speed) by cams or unbalanced weights , High pressure grinding ...
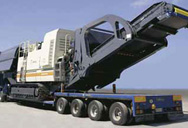
Forest Product Roll Grinding | Precision Roll Grinders
The roll grinding services at PRG guarantee round rolls with tolerances of up to +/- 20 millionths of an inch, providing numerous benefits to your mill’s production such as improved product quality, very uniform product thickness due free of sander roll defects, improved process efficiency, reduced downtime due to unplanned maintenance and equipment failure, and reduced waste and energy ...
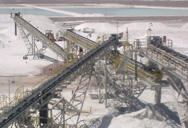
Rolling process animation || Rolling mill machine …
18-10-2017 · ️First of all, Happy diwali to all my subscribers and viewers as well.️ Hello guys, I welcome you again in this new fresh topic. This topic is regarding the rolling process used for ...
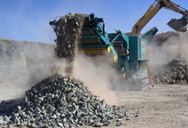
Non-circular grinding of backup rolls to reduce rolling ...
external roll surface for a non-circular geometry capable of reducing the fluctua-tion of the roll force in the rolling process. A new method to minimize force variations, based on 3D grinding of the mill rolls, was developed [3]. Finite element models, describing the backup roll
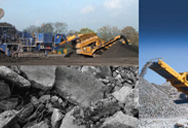
Paper machine roll maintenance | Valmet
Our 360°Rolls view takes into account the entire roll environment, for example, we focus on how the fabrics, roll covers and doctor blades perform together in the process. Through a combination of extensive roll technology expertise and in-depth process know-how, modular maintenance solution eliminates unplanned shutdowns and maximizes roll maintenance intervals.
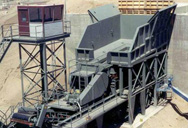
Mill (grinding) - WikiMili, The Free Encyclopedia
Ball mills are commonly used in the manufacture of Portland cement and finer grinding stages of mineral processing, one example being the Sepro tyre drive Grinding Mill. Industrial ball mills can be as large as 8.5 m (28 ft) in diameter with a 22 MW motor, [4] drawing approximately 0.0011% of the total worlds power (see List of countries by electricity consumption ).