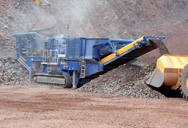
Molybdenum: mining and processing-Metalpedia
Molybdenum mines are classified into three groups according to the minerals contained in the ore body and their quality: •Primary mines, where the extraction of molybdenite is the sole aim. •By-product mines, where the extraction of copper-bearing ores is the primary aim, and molybdenite extraction provides additional economic value. •Co-product mines, where both molybdenite and copper-bearing …
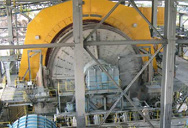
Molybdenum Processing - IMOA: International …
Flotation separates the metallic minerals from the gangue this way and – in the case of copper/ molybdenum ores – separates molybdenite from copper sulphide. The resulting MoS 2 concentrate contains between 85% and 92% MoS 2 .
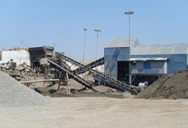
Molybdenum processing | Britannica
Molybdenum processing, preparation of the ore for use in various products. Molybdenum (Mo) is a white platinum-like metal with a melting point of 2,610 °C (4,730 °F). In its pure state, it is tough and ductile and is characterized by moderate hardness, high thermal conductivity, high resistance to corrosion, and a low expansion coefficient.
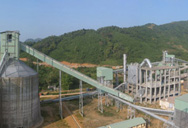
molybdenite processing - das-astra.de
Molybdenite polytypism and its impliions for processing . A geometallurgical investigation was undertaken of molybdenite from the Bingham Canyon deposit with the aim of determining what effects, if any, mineralogy and the mineralogical attributes of morphology, angularity, liberation and size have on molybdenite recovery in the processing circuit.
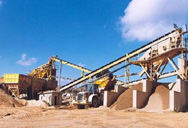
Molybdenite Processing
In molybdenite processing, the molybdenite is first heated to a temperature of 700 °C (1,292 °F) and the sulfide is oxidized into molybdenum(VI) oxide by air: 2 MoS2 + 7 O2 → 2 MoO3 + 4 SO The oxidized ore is then either heated to 1,100 °C (2,010 °F) to sublimate the oxide, or leached with ammonia, which reacts with the molybdenum(VI) oxide to form water-soluble molybdates: MoO3 + 2 ...
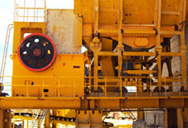
molybdenite processing - Mine Equipments
Chemical processing of a low grade molybdenite concentrate to ... Abstract. The conventional oxidative roasting process, as applied to high grade molybdenite …
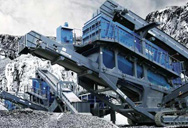
Molybdenum Mining and Processing
Molybdenum mining and processing techniques have been improved continuously since the first mine was started at Climax near Leadville, Colorado in 1916. Today, the principal moly mines, both primary and by-product, are found along the Great Continental Divide of the Americas, in China and in the CIS. Many of these mines are amongst the most productive in the world, with the largest capable of ...
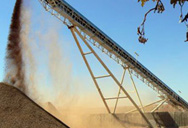
Molybdenum Processing | Equipment, Process …
Molybdenum was discovered by Carl Wilhelm Scheele in 1778, and was isolated and named by Peter Jacob Hjelm in 1781. The most important ore source of molybdenum is the mineral molybdenite; a minor amount is recovered from the mineral wulfenite. Molybdenum commonly is recovered as a by-product or co-product from copper mining. The U.S. produces ...
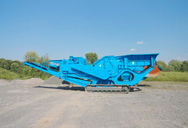
Mining - Molybdenum
Molybdenum is contained in various minerals, but only molybdenite (MoS 2) is suitable for the industrial production of marketable molybdenum products. Molybdenite can occur as the sole mineralization in an ore body, but is often associated with the sulphide minerals of other metals, notably copper. The Mo content of viable ore bodies ranges between 0.01 and 0.25%.

Molybdenite - Wikipedia
Molybdenite occurs in high temperature hydrothermal ore deposits. Its associated minerals include pyrite, chalcopyrite, quartz, anhydrite, fluorite, and scheelite. Important deposits include the disseminated porphyry molybdenum deposits at Questa, New Mexico and the Henderson and Climax mines in Colorado. Molybdenite also occurs in porphyry copper deposits of Arizona, Utah, and Mexico. The element rheniumis always present in molybdenite as a substitute for molybdenum, usually in the pa…
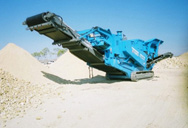
Molybdenum Ore Processing by Flotation
Molybdenum Ore Processing by Flotation. How to separate copper & molybdenum; the problem. Molybdenum is found in small amounts in practically all low grade porphoritic copper ores. It is usually present as the sulphide, molybdenite, which is readily recovered in the copper flotation concentrate. Copper sulphide flotation concentrates may contain from 0.25 to 1.00% MoS2. When such ores are ...
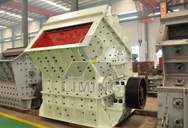
Molybdenite Flotation - Metallurgist & Mineral …
The process recommended for industrial recovery of molybdenite from copper concentrates is expected to yield a product grade of not less than 45% Mo with a recovery of minimum 65%. The final concentrate can be de-copperized by ferric chloride leaching.
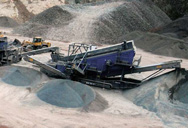
Molybdenite: Mineral information, data and …
Variations of the name molybdaena and molybdenite were used for lead ores by Dioscorides (50-70 CE), Pliny the Elder (79 CE), and Agricola (1556), but the modern use of molybdenite did not begin until Johan Gottschalk Wallerius wrote about molybdenite in Mineralogia, eller Mineralriket published in 1747. There was still a multiplicity of minerals receiving the same name, but modern molybdenite ...
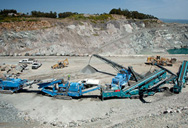
Molybdenum Roasting - Mineral Processing & …
Molybdenite MHR – Advantages. Multiple Hearth Roasters are available reliable furnaces. Roasting reactions are slowed allowing for furnace temperature control. SO2 off-gas can be fed to recovery processes which also produce a salable by-product. (Sulfuric Acid) Existing equipment is utilized with non-exotic materials of construction.
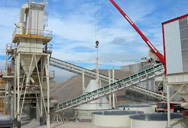
molybdenite processing - scalepaint-dioramas.nl
In molybdenite processing, the ore is first roasted in air at a temperature of 700 °C (1,292 °F). The process gives gaseous sulfur dioxide and the molybdenum(VI) oxide: 2 MoS 2 + 7 O 2 → 2 MoO 3 + 4 SO 2. Read more . INVESTIGATION OF EFFECTIVE PARAMETERS FOR . Molybdenite reserves of the world are distributed in eight countries such as China, USA, Chile, Canada, Russia, Armenia, …
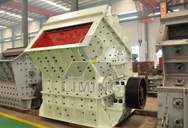
Processing Molybdenite Concentrate by an Acid …
As one would expect, product grade decreased as the grade of the plant feed decreased. Each 10 percent decrease in the molybdenite assay of the plant feed decreased the product grade 1. 5 percent within the 40 to 80 percent molybdenite feed concentration range studied.