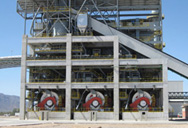
Cement mill - Wikipedia
A cement mill (or finish mill in North American usage) is the equipment used to grind the hard, nodular clinker from the cement kiln into the fine grey powder that is cement.Most cement is currently ground in ball mills and also vertical roller mills which are more effective than ball mills.
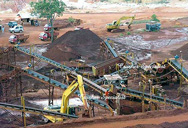
Optimum clinker temperature for cement mill
Optimum clinker temperature for cement mill. optimum clinker temperature for cement mill the clinker grinding in the cement mills is an essential process where the effect of clinker temp in cement grinding effect of temperature during cement grinding Get Price cement ball mill page 1 of 2 · re cement ball mill hi what is the maximum of the clinker size entering first chamber what

What should be the outlet temperature of cement …
The cement factory convey cement from cement mill to cement silos by open belt conveyors. I need to know what is temperature loss of cement in belt conveyor if it takes 3 to 4 min to reach the ...
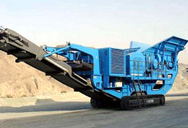
PROCESS DIAGNOSTIC STUDIES FOR CEMENT MILL …
CEMENT MILL OPTIMISATION - CASE STUDY V.K. Batra*, ... Separation air at separator outlet : 5599 m 3/min Separator vent air at bag filter outlet : 210 m 3/min ... − Water spray is being done into the 2nd Chamber of the mill even though the cement temperature is
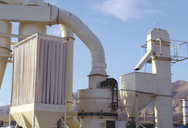
how much maintain the cement temperature at …
Cement Kilns: Raw Material Preparation When heated to the peak temperature in the kiln, "clinkering" takes place. .... in this case the mill is designed primarily to keep the flints in violent motion, and these in ....Much closer to the modern idea of a ball mill was the tube mill. ...diaphragm at the outlet and was lifted into the outlet trunnion with scoops Tube mills were ...
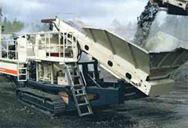
High Exit vent temp at cement mill outlet - Page 1 …
2-11-2015 · High Exit vent temp at cement mill outlet. We have open circuit ball mill grinding OPC 43 grade, feed moisture 2% max, Inlet temp 35 Deg C and outlet temp we are getting around 90 to 95 deg C, what could be the reason of high temp at mill outlet, since we have not supplied hot gas at feed, can anybody suggest the possible reason please, which helps to take necessary action.
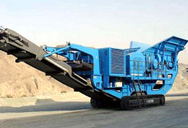
Water injection system - WIS™ | Magotteaux
Optimize your grinding process via temperature control Water injection is one way to control and maintain the cement temperature at mill outlet at a preset level. Depending on the circuit thermal balance analysis and the mill design, Magotteaux water injection system (WIS™) automatically sprays water into the mills in 3 different ways: 1st chamber via its inlet 2nd chamber via mill outlet or ...
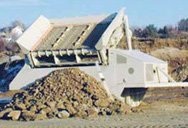
Cement Milling - Understanding Cement
Cement milling is usually carried out using ball mills with two or more separate chambers containing different sizes of grinding media (steel balls). Grinding clinker requires a lot of energy. How easy a particular clinker is to grind ("grindability") is not always easy to predict, but large clusters of belite due to coarse silica in the feed are difficult to grind.

Cement Grinding - Cement Plant Optimization
Cement discharge temperature should be kept below about 110 o C but, the same time should allow some 60% dehydration of gypsum to optimize cement strength without excessive false set. Water spray is controlled with mill outlet gas or material temperature.
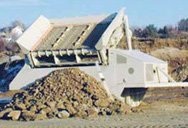
Boiler Performance and Mill Outlet Temperature - …
Two major parameters which decide the mill capacity and performance are the hardness of coal and the total moisture level in coal. The mill outlet temperature of coal-air mixture is maintained between 65 to 90 degree centigrade in the case of low and medium volatile coal. In the case of high volatile coal while the lower limit generally remains as 65 degree centigrade, the upper limit is ...
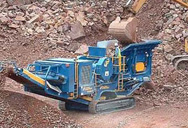
Suitable temperature for cement storage in silo …
Suitable temperature for cement storage in silo and also for better roto packer performance. Dear sir, Please let me Know the Suitable temperature for cement storage in silo and also for better roto packer performance as we are facing silo extraction and frequent nozzle jamming of roto packer in line -2 where cement grinding is being done Verticle mill and mill outlet temperature is being ...
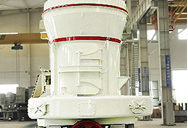
Monitoring Control Systems for Cement Plants
Mill outlet temperature control Mill rotation speed control Burning Kiln rotation speed control Kiln hood draft control Tertiary airfl ow control Cooler two chamber pressure control Preheater induction draft fan (IDF) damper control Finishing Clinker and gypsum fl ow control Finish mill monitoring Finish mill separator control Cement ...
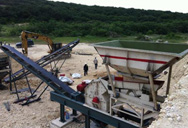
Rawmill - Wikipedia
A raw mill is the equipment used to grind raw materials into "rawmix" during the manufacture of cement. Rawmix is then fed to a cement kiln, which transforms it into clinker, which is then ground to make cement in the cement mill.The raw milling stage of the process effectively defines the chemistry (and therefore physical properties) of the finished cement, and has a large effect upon the ...
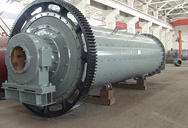
Cement kiln - Wikipedia
Cement kilns are used for the pyroprocessing stage of manufacture of Portland and other types of hydraulic cement, in which calcium carbonate reacts with silica-bearing minerals to form a mixture of calcium silicates.Over a billion tonnes of cement are made per year, and cement kilns are the heart of this production process: their capacity usually defines the capacity of the cement plant.
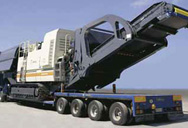
Heat balance calculators
The calculation of the thermical balance of the ball mill is now proposed according 2 methods: - The first method, we know the ventilation of the mill + the cement temperature and we want to calculate the water quantity we need to inject in order to get the temperature at mill outlet we would like to have.
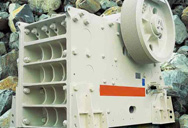
8 FACTORS AFFECTING SETTING & HARDENING …
But if the temperature is under 0 0 C, the hydration of cement will stop and the strength will not only stop growing but also destroy the structure of cement paste due to the condensation of water. In actual projects, the setting and hardening process of cement products is accelerated by steam curing and autoclave curing.
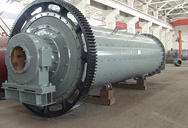
Cement kiln - Wikipedia
Cement kilns are used for the pyroprocessing stage of manufacture of Portland and other types of hydraulic cement, in which calcium carbonate reacts with silica-bearing minerals to form a mixture of calcium silicates.Over a billion tonnes of cement are made per year, and cement kilns are the heart of this production process: their capacity usually defines the capacity of the cement plant.
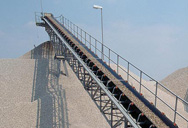
Electrostatic precipitators (ESP) - FLSmidth
We design electrostatic precipitators for use with clinker coolers with or without waste heat recovery in the circuit for a temperature range of 90-400°C. Our deep process knowledge of dust behaviour associated with kilns and raw mills, including how to return dust to the process, has resulted in an effective, highly compact ESP design, which minimises footprint.